Welcome to our comprehensive guide on understanding labor costs for fence installation! If you’re considering adding a fence to your property, you’re likely wondering how much labor will cost and what factors affect the final price. Installing a fence can boost your home’s privacy, security, and curb appeal, but getting a clear estimate on labor can be tricky due to the various materials, designs, and yard conditions involved. In this post, we’ll break down the typical labor costs, what you can expect based on different factors, and tips for budgeting your project effectively. Whether you’re looking to hire a pro or take the DIY route, this guide will help you make an informed decision.
On average, labor for fence installation costs between $30 to $70 per hour, or approximately $5 to $15 per linear foot, depending on factors such as fence type, project complexity, and local rates.
Table of Contents
Understanding Labor Costs For Fence Installation
When it comes to installing a fence, labor costs are one of the most significant expenses you’ll face. Whether you’re fencing in a garden, adding privacy, or securing your property, understanding what goes into the labor and how it’s priced can help you budget more effectively. Let’s dive into the essential components of labor costs, what’s typically included, and how much you might expect to pay depending on your location and fence type.
What Is Included in Labor for Fence Installation?
The labor involved in installing a fence covers a range of tasks, each requiring time, skill, and precision. Here’s a detailed breakdown of what the labor process typically includes:
1. Setting Fence Posts: This is the foundational step. Fence posts must be dug, leveled, and secured properly. The depth and width of the holes vary depending on the type of fence and local regulations.
2. Installing Fence Panels: Once the posts are secure, the next step is attaching the fence panels or individual pickets. This task requires careful alignment to ensure the fence looks even and functions properly.
3. Leveling and Securing the Fence: Ensuring that the fence is level is crucial for both aesthetics and stability. Labor costs also account for securing the panels and posts firmly to withstand weather conditions.
4. Clean-Up and Post-Installation Inspection: After the installation, the site must be cleared of debris. Contractors will also inspect the fence to ensure that everything meets safety and quality standards.
Average Labor Costs Across the U.S
Labor costs for fence installation can vary significantly based on location, the complexity of the project, and the specific fence material used. Here’s a look at the average labor cost range across the United States:
- National average cost range: Expect to pay between $30–$70 per hour for labor, or $5–$15 per linear foot. This range can shift depending on various factors, including the region and type of fence being installed.
- Regional variations: Urban areas often have higher labor costs due to the increased cost of living and demand for services. Conversely, rural areas tend to offer lower labor costs. For example, a simple chain link fence in a rural setting might cost less to install than a more intricate wrought iron fence in a metropolitan area.
- Project complexity: The more complex the fence installation, the higher the labor costs. Obstacles like uneven terrain, difficult access, or special designs can drive up both the time and cost of installation.
Labor Cost Breakdown by Fence Type
Different fence materials not only affect the cost of materials but also labor. Here’s a detailed overview of labor costs broken down by fence type:
1. Wood Fence
- Labor and Material Cost: $10–$25 per linear foot
- Description: Wood fences, like picket or privacy fences, are one of the more affordable options. However, they require precise installation to prevent warping or uneven alignment, especially with natural wood.
2. Vinyl Fence
- Labor and Material Cost: $15–$30 per linear foot
- Description: Vinyl fences are more expensive than wood but require less maintenance. Installation typically involves pre-formed panels, making it a bit faster, but they still require careful securing and alignment.
3. Chain Link Fence
- Labor and Material Cost: $5–$20 per linear foot
- Description: Chain link fences are among the least expensive to install. They are often used for security or defining property lines and can be installed relatively quickly, leading to lower labor costs.
4. Wrought Iron/Aluminum Fence
- Labor and Material Cost: $25–$40 per linear foot
- Description: Wrought iron or aluminum fences are highly durable and add a touch of elegance to a property. However, they are heavier and more intricate to install, which increases labor costs. The metalwork often requires specialized tools and skills, adding to both time and expense.
Key Takeaways for Each Fence Type
- Wood fences are affordable but labor-intensive due to their natural material and need for precise alignment.
- Vinyl fences offer a balance between cost and durability, with moderately priced labor but higher material costs.
- Chain link fences provide a low-cost option for labor, ideal for larger areas where budget is a concern.
- Wrought iron and aluminum fences are the most expensive in terms of labor due to their weight and complexity, but they offer unmatched durability and aesthetic appeal.
Understanding the labor costs for fence installation is crucial for budgeting any fencing project. Labor typically covers several steps, from post-setting to final inspection, and the price you pay will depend largely on your location and the type of fence you choose. Whether you’re opting for an affordable chain link fence or a high-end wrought iron option, knowing the expected labor costs can help you plan and make informed decisions. By keeping these factors in mind, you’ll be better prepared to choose the right fence for your property while staying within your budget.
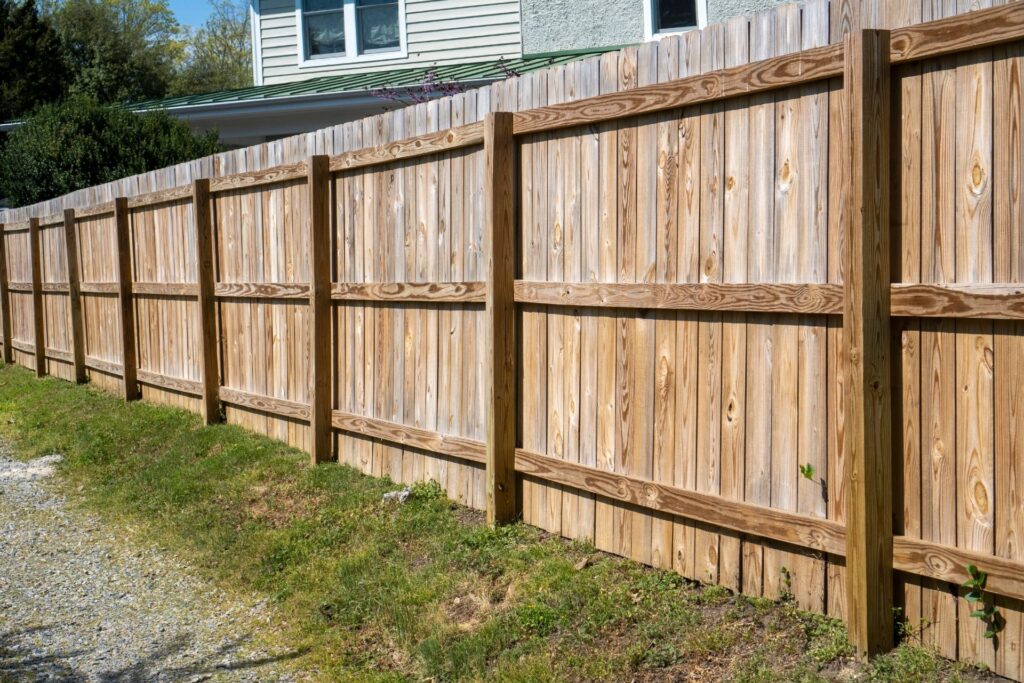
Factors That Affect Labor Costs For Fence Installation
When planning a fence installation, labor costs can significantly vary depending on several key factors. Understanding these factors helps homeowners make informed decisions, potentially optimizing their budget and managing expectations. Below is an in-depth look at the primary aspects that influence labor costs for installing a fence.
1. Fence Material
The type of material you choose for your fence is one of the biggest factors in determining labor costs. Different materials require varying levels of effort to install.
- Wood vs. Wrought Iron or Vinyl: Wood is often a more affordable fencing material compared to wrought iron or vinyl. This price difference is due not only to the cost of the materials themselves but also to the labor required for installation. Wood is lighter and easier to work with, allowing for quicker and simpler installations. In contrast, wrought iron and vinyl are heavier and often more complex to install, requiring more time and effort. For example, wrought iron typically involves more precision work and may need specialized tools, increasing labor hours and costs.
- Custom Materials: If you opt for custom fencing materials, such as bamboo or composite, the labor cost may increase. Custom materials often require additional handling, specific installation techniques, and more time-consuming processes, all of which add to the overall labor expense.
2. Terrain and Yard Conditions
The condition of your yard and the type of terrain can significantly affect labor costs.
- Flat vs. Sloped or Rocky Ground: Installing a fence on flat terrain is generally straightforward and requires less labor. However, if your yard is sloped or rocky, workers will need to spend more time leveling the ground or adjusting the fence to accommodate uneven surfaces. This can involve additional digging, grading, or the use of specialized equipment, all of which contribute to increased labor hours and costs.
- Difficult Soil and Roots: Soil composition plays a role as well. For example, clay or rocky soil can be harder to dig through, requiring more effort and time. If workers encounter large roots or rocks while digging post holes, this can also slow down the process and increase labor expenses.
3. Fence Design and Style
The complexity of your fence design will directly impact labor costs.
- Pre-fabricated Panels vs. Custom Designs: Pre-fabricated fence panels are easier and faster to install because they come ready to assemble. This reduces labor hours and overall installation time. On the other hand, custom-designed fences, which may involve cutting, fitting, and precise measurements, require more time and skill, increasing labor costs.
- Decorative Elements: If you want to add decorative elements like caps, lattice, or other intricate features, expect the labor costs to rise. These custom additions take extra time and effort, as workers need to carefully install them to achieve the desired aesthetic.
4. Length and Height of the Fence
The size of your fencing project has a direct correlation with labor costs.
- Length: The longer the fence, the more labor is required to install it. Each section of the fence must be measured, posts dug, and panels or boards installed, meaning a longer fence will take more time and increase labor expenses.
- Height: A taller fence also requires more effort to install. Taller posts need to be secured deeper into the ground, and handling larger materials takes more time. Additionally, local regulations may require extra safety measures for taller fences, such as bracing or reinforced posts, further increasing labor costs.
5. Permits and Local Regulations
Obtaining permits and adhering to local regulations can also affect labor costs.
- Permits: Depending on your location, you may need to acquire permits before installing a fence. In some areas, fence installation may require inspections at different stages of the process, such as after post holes are dug or after the fence is completed. Coordinating with local inspectors adds time to the project, which in turn affects labor costs.
- Additional Safety Measures: Some locations have specific requirements for fencing, such as additional safety measures for fences near pools or in high-wind areas. Meeting these regulations can increase the complexity of the installation and the associated labor costs.
6. Access to Worksite
The ease with which workers can access the installation site can also impact labor costs.
- Easy Access vs. Hard-to-Reach Areas: If the worksite is easily accessible, materials and tools can be transported quickly and efficiently, keeping labor costs down. However, if your backyard is difficult to reach, for example, due to narrow side yards or other obstructions, workers may need to take more time to transport materials to the fence line, increasing labor time and costs.
- Tight Spaces: In cases where space is limited, such as in a crowded urban environment or a small backyard, the installation process can become more challenging. Workers may need to use specialized equipment or techniques to maneuver in tight spaces, which adds to the labor cost.
Understanding the factors that affect labor costs for fence installation can help homeowners plan and budget for their projects more effectively. From material selection to yard conditions and design choices, each decision can have a direct impact on the overall labor expenses. By considering these aspects upfront, you can ensure that your fence installation runs smoothly while staying within your budget.
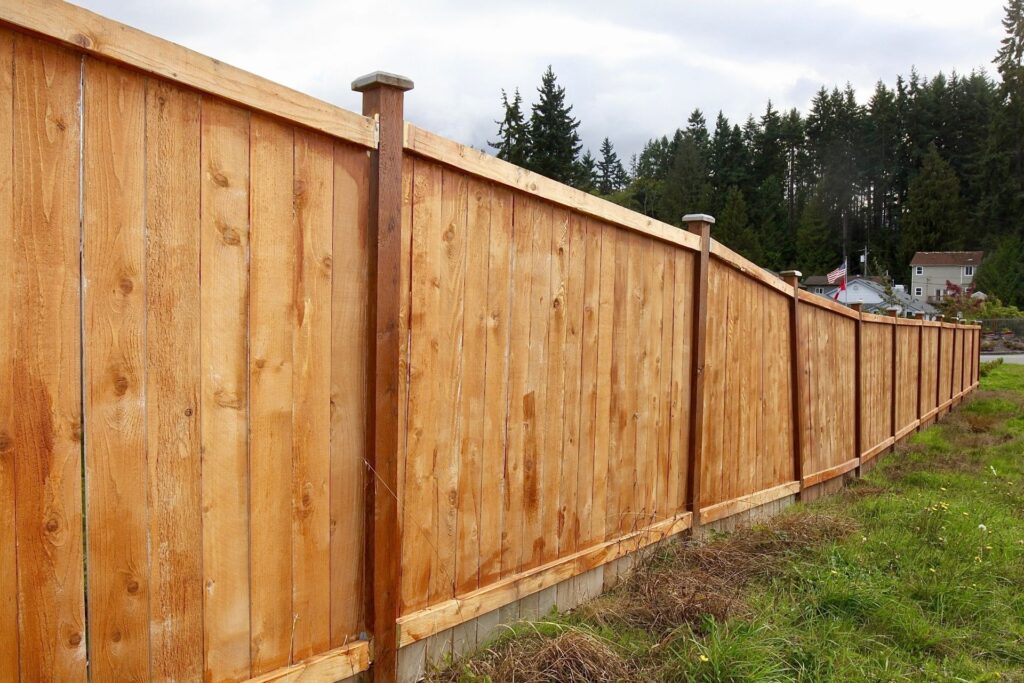
DIY Vs. Hiring A Professional Installer
When it comes to fence installation, homeowners face a crucial decision: Should you tackle the project yourself or hire a professional? Each approach has its own set of advantages and drawbacks, and what works best depends on your budget, skills, and time commitment. Let’s dive into the key factors to consider.
1. Pros and Cons of DIY Fence Installation
Pros:
One of the biggest benefits of DIY fence installation is cost savings. Labor typically represents a significant portion of the total cost of hiring a professional. By doing it yourself, you can eliminate that expense, potentially saving hundreds or even thousands of dollars depending on the size of the project. For those with a good amount of experience and the right tools, DIY can be a satisfying, hands-on way to enhance your property.
Cons:
However, DIY fence installation comes with its own set of challenges. First, it’s highly time-consuming, particularly for those new to this type of work. Even smaller fence projects can take multiple days or even weeks to complete, depending on your availability. Another challenge is the skill requirement—from precise measurements to proper post-hole digging, any mistake can lead to an unstable fence or costly rework. Tasks like ensuring the posts are aligned and evenly spaced can be difficult for someone without experience. The actual physical labor, especially in harder soil conditions or when dealing with slopes, can also be tough.
Common DIY Challenges:
Some typical challenges DIYers face include digging post holes deep enough to provide stability, properly aligning and leveling posts, and handling heavy materials. Mistakes here can compromise the fence’s durability and appearance, leading to costly repairs down the road. For example, failing to secure posts at the correct depth may result in leaning or unstable fences after a few seasons of weather exposure.
2. Why Hiring a Professional May Be Worth the Cost
Expertise and Faster Installation
Hiring a professional contractor brings expert knowledge and experience to the table. Fence installation might seem straightforward, but it involves many technical details that professionals have mastered. This means a professional team can complete the job much faster than a DIYer, often within a couple of days, even for larger projects. Time savings alone can justify the cost for many homeowners, especially those with busy schedules.
Lower Risk of Mistakes
With professionals, you reduce the likelihood of errors. Since contractors install fences for a living, they are less likely to make the mistakes that can plague DIY installations—such as uneven post placement, incorrect measurements, or improper securing of materials. These errors can result in the fence being less sturdy, which might necessitate expensive fixes in the future. In many cases, professional installations come with warranties, offering peace of mind if something goes wrong.
Better Equipment and Tools
Professional installers come equipped with specialized tools, such as post-hole diggers, augers, and laser levels, which allow them to work more efficiently and accurately. These tools may be expensive or impractical to purchase for a one-time DIY project. Additionally, their expertise means they can navigate challenging terrains or unexpected issues (like rocky soil or underground utilities) with minimal hassle.
3. Finding the Right Fence Contractor
If you decide to hire a professional, finding the right contractor is essential to ensure the job is done correctly and on budget.
Tips for Vetting Contractors:
- Check Licenses and Certifications: Make sure any contractor you’re considering is properly licensed and insured. This protects you in case of accidents or damage during the installation.
- Read Reviews and Ask for References: Online reviews can provide insights into the contractor’s professionalism and quality of work. Ask for references from recent clients to get a better idea of their work history.
- Get Multiple Quotes: Don’t settle for the first estimate. Request quotes from several contractors to compare pricing, timelines, and services. This will also help you avoid inflated rates or hidden fees.
Accurate Quotes and Hidden Fees:
Be wary of any contractor who provides a vague or incomplete quote. A reputable professional will give you a detailed estimate that breaks down labor, materials, and any potential additional costs (e.g., permits, disposal fees). Be sure to ask about any additional costs that might arise so you’re not caught off guard.
Deciding between a DIY fence installation and hiring a professional depends on various factors, including your budget, time, and experience level. While DIY can offer cost savings, it also comes with significant challenges and the potential for mistakes. On the other hand, hiring a professional ensures a faster, more reliable installation but comes at a higher cost. Whichever option you choose, taking the time to weigh the pros and cons will help you make the best decision for your home and your fence project.
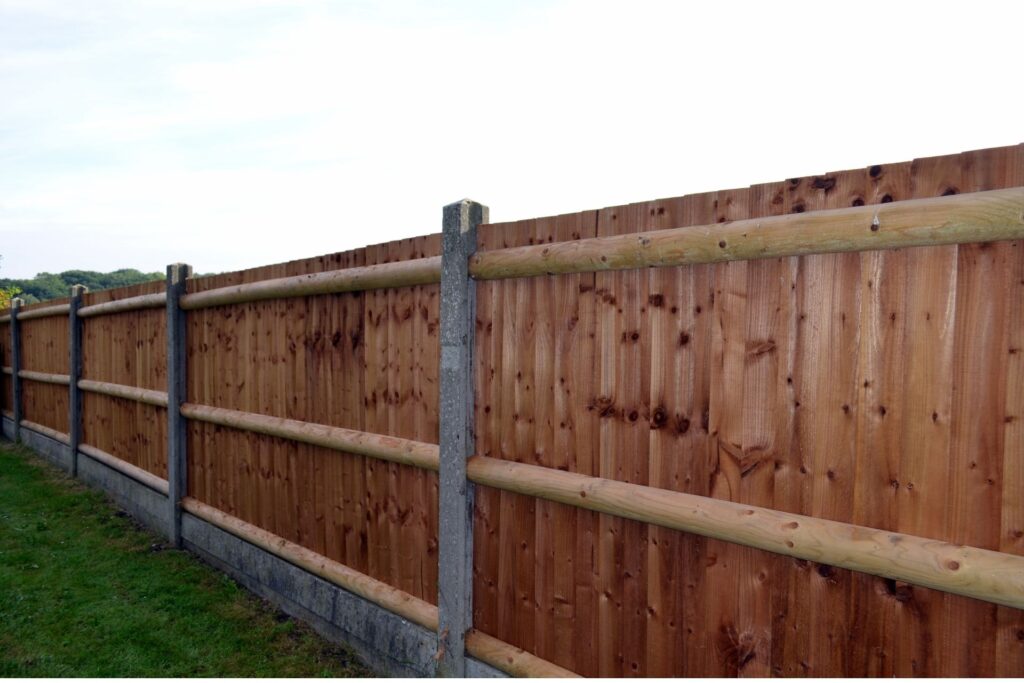
Hidden Costs To Watch Out For
When planning a fence installation, it’s easy to focus on the material and labor expenses, but there are often hidden costs that can sneak up on you if you’re not prepared. These unexpected fees can significantly impact your overall budget, so it’s crucial to know what to look for. Below are some of the most common hidden costs to watch out for when installing a new fence.
1. Removal of Old Fence
Before your new fence goes up, you’ll need to remove the old one, and this process isn’t always as simple or as cheap as it might seem. The cost of removing an existing fence can vary depending on its size, material, and the labor involved. If the fence is large or made of heavier materials like iron or thick wood, labor costs may increase due to the time and effort required for dismantling it.
Additionally, there are disposal fees to consider. Not all contractors include debris disposal in their quotes, and dumping fees can add up, especially if the old fence is bulky or contains hazardous materials like lead paint. Always confirm whether removal and disposal are included in your installation quote, or you might find yourself facing unexpected expenses.
2. Unforeseen Issues
During fence installation, you may run into unforeseen obstacles that can drive up costs. One of the most common issues is hitting underground utility lines or tree roots when digging post holes. If a utility line is struck, not only can it cause delays, but you could also be responsible for expensive repairs, depending on local laws. Always ensure you have a utility survey completed before installation begins to avoid this costly mistake.
Additionally, if your property has drainage issues or uneven landscaping, your contractor may need to address these problems before or during fence installation. For instance, fixing water drainage issues might require adding gravel or re-grading a section of the yard. These additional tasks can quickly inflate your overall costs, so it’s wise to discuss any potential issues with your contractor beforehand.
3. Customization Costs
Customizing your fence can enhance its functionality and aesthetic appeal, but these features often come at an extra cost. If you’re thinking of adding gates, especially automated or custom-designed gates, expect to pay more. The complexity of installation increases with gates, as they may require additional materials, hinges, and labor, especially if the ground is uneven.
Adding decorative elements such as post caps or ornamental details can also raise your final bill. While these features make your fence more attractive, they involve additional time and materials that your contractor will likely charge for. Similarly, if you’re installing security features like locks, sensors, or security cameras, this adds another layer of cost. These upgrades often require specialized labor and extra hardware, contributing to a higher total expense.
By keeping these hidden costs in mind, you can better plan for your fence installation and avoid surprises that could blow your budget. Always ask your contractor for a detailed quote that includes potential extra fees, so you can stay one step ahead of unexpected expenses.
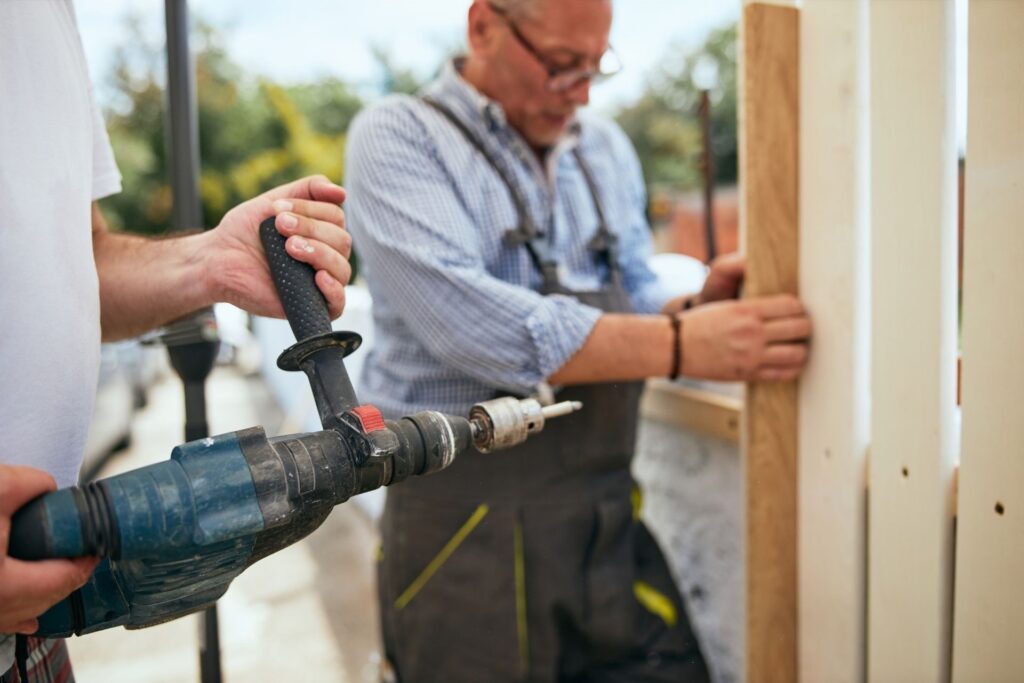
How To Save On Labor Costs For Fence Installation
Saving on labor costs during fence installation is a priority for many homeowners looking to get the most value for their investment. Whether you’re working with a contractor or handling part of the job yourself, there are several strategies you can use to reduce expenses without compromising on quality.
1. Get Multiple Quotes
One of the simplest yet most effective ways to save on labor costs is to gather multiple quotes from different contractors. Each contractor may offer a unique breakdown of pricing, so it’s essential to compare them carefully. When reviewing quotes, pay attention to what’s included in the labor cost. Some contractors may bundle services such as site preparation, removal of old fencing, or post-installation cleanup, while others might charge separately for these tasks. Make sure you’re comparing apples to apples by checking the specifics of each quote and not just the bottom-line price.
Furthermore, asking about labor guarantees or warranties on workmanship is essential. This can save you money down the road if any issues arise after the installation is complete. Taking the time to evaluate multiple options gives you a clearer picture of fair pricing and helps you avoid overpaying.
2. Time Your Installation
Timing can significantly impact labor costs, especially when it comes to seasonal fluctuations. Most people choose to install fences in the spring and summer when the weather is ideal. However, these are also the busiest seasons for contractors, which can drive up labor costs. Opting to schedule your fence installation in the off-season—typically fall or winter—can lead to substantial savings. During these slower months, contractors are often more flexible and may offer discounts to secure work.
While weather conditions in fall or winter may not seem ideal for construction, many types of fencing, especially those made of materials like vinyl or metal, can still be installed successfully. Just be sure to consult with your contractor to ensure the timing won’t affect the integrity of the installation.
3. Opt for Simple Designs
The complexity of your fence design can directly impact the number of labor hours required for installation. Elaborate designs with intricate details, curves, or custom elements typically take more time and skill to install, leading to higher labor costs. Opting for a simple, straightforward design can significantly reduce the time spent on the job, thereby lowering labor expenses.
For instance, a basic picket fence or a straightforward privacy fence with standard panels will take less time to install compared to a fence with decorative elements or complex patterns. If you’re open to it, scaling back on design details can keep labor costs manageable while still giving you a functional and attractive fence.
4. DIY for Part of the Job
Another great way to cut labor costs is by taking on some of the work yourself. While you may not want to handle the technical aspects of fence installation, there are several tasks you can manage to reduce the contractor’s workload. For example, clearing the site of debris, rocks, or old fencing can save time and money. Additionally, buying your materials ahead of time—whether it’s wood, metal, or vinyl fencing—can often be less expensive than purchasing them through a contractor.
If you’re confident in your skills, you could even consider setting posts or doing other basic prep work yourself. However, if you’re unsure of your abilities or don’t have the necessary tools, it’s wise to leave the more technical parts of the job, like leveling and installing the panels, to the professionals. Even handling part of the work can significantly reduce the overall cost.
5. Consider Group Projects
If you and your neighbors are all considering installing new fences, you might be able to take advantage of group discounts. Contractors are often willing to offer reduced labor rates when they can work on multiple projects at the same time in the same location. This approach saves them time on travel, setup, and site preparation, and they often pass those savings on to their clients.
Organizing with neighbors not only helps you save money but can also lead to a more uniform look across properties, increasing curb appeal for the entire neighborhood. Group discounts can be especially appealing in suburban areas where many homes require fencing or fencing repairs.
By following these strategies, you can effectively lower labor costs during your fence installation. Whether through careful planning, doing some of the work yourself, or taking advantage of seasonal discounts and group rates, there are plenty of ways to save without sacrificing the quality or durability of your fence.
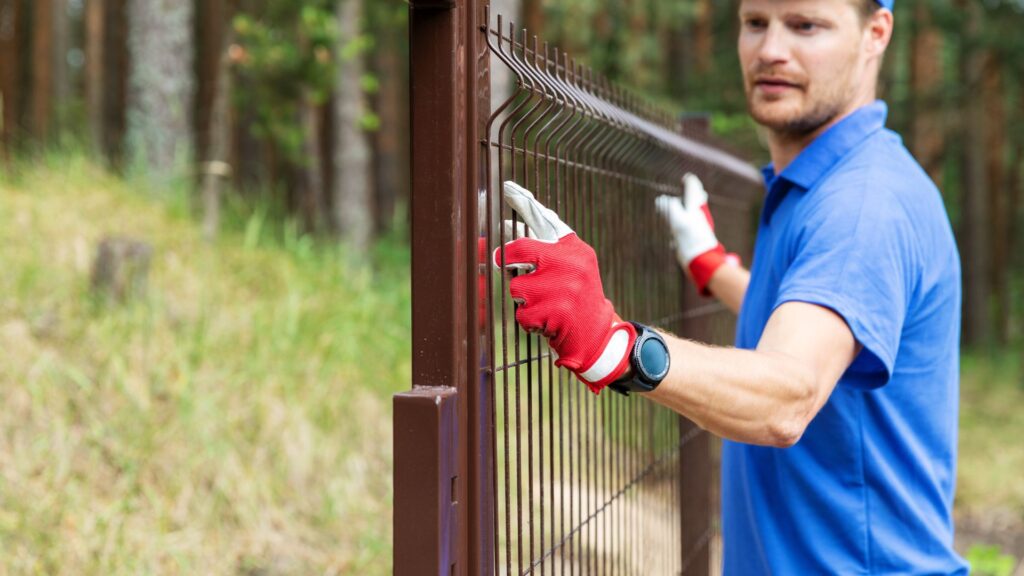
FAQs: About How Much Is Labor For Fence Installation
How much does labor cost to install a 100-foot fence?
Labor costs for a 100-foot fence typically range from $500 to $1,500, depending on factors like fence type, terrain, and complexity. This assumes labor charges of $5 to $15 per linear foot.
What factors affect the cost of fence installation labor?
The cost of labor for fence installation can be influenced by several factors, including the type of fence material, terrain (flat or sloped), the length and height of the fence, accessibility of the installation site, and any custom designs or features you choose.
Is it cheaper to install a fence myself?
Yes, installing a fence yourself can save you on labor costs, which typically account for a large portion of the total expense. However, keep in mind that DIY projects require time, skill, and tools, and mistakes can be costly to fix.
How long does it take to install a fence?
A professional fence installation can take anywhere from 1 to 3 days, depending on the size of the project, the complexity of the fence design, and weather conditions. DIY installations may take longer, particularly for those unfamiliar with the process.
What is the most affordable type of fence to install?
Chain link fences are typically the most affordable to install, with labor costs averaging between $5 and $20 per linear foot. Vinyl and wood fences tend to cost more due to the materials and additional labor involved.
Do I need a permit to install a fence?
In most areas, you will need a permit to install a fence, especially if the fence is over a certain height. Your local zoning laws will specify the requirements. Some contractors handle permits as part of their service, so be sure to ask if it’s included in their fees.
Can I negotiate labor costs with a fence contractor?
Yes, you can often negotiate labor costs with fence contractors, especially if you’re installing a large fence or if you’re flexible with the timing. Getting multiple quotes can help you compare rates and negotiate a fair price.
What additional costs should I expect when installing a fence?
Additional costs can include removing old fencing, clearing the site, obtaining permits, and any unexpected issues like hitting utility lines or dealing with difficult terrain. Custom features, such as gates or decorative elements, can also increase labor and material costs.
What should I look for when choosing a fence contractor?
When choosing a fence contractor, look for licensed and insured professionals with good reviews and references. Make sure to get detailed quotes that clearly outline labor and material costs, and check their portfolio to ensure they have experience with your chosen fence type.
How can I reduce the cost of fence installation labor?
You can reduce labor costs by preparing the site before the contractor arrives, such as clearing the area or removing an old fence. Choosing a simpler fence design, installing the fence during the off-season, and getting multiple quotes can also help you save on labor.
Conclusion
In conclusion, the cost of labor for fence installation can vary based on several factors, such as the type of material, the complexity of the job, and the size of the project. Homeowners who take the time to understand these aspects will be better equipped to make informed decisions that suit their budget and needs. If you have any questions or experiences you’d like to share, feel free to leave a comment below. And when you’re ready to begin your fence project, don’t hesitate to reach out to trusted professionals for a quote to get started.
About the Author:
Mike Veail is a recognized digital marketing expert with over 6 years of experience in helping tradespeople and small businesses thrive online. A former quantity surveyor, Mike combines deep industry knowledge with hands-on expertise in SEO and Google Ads. His marketing strategies are tailored to the specific needs of the trades sector, helping businesses increase visibility and generate more leads through proven, ethical methods.
Mike has successfully partnered with numerous companies, establishing a track record of delivering measurable results. His work has been featured across various platforms that showcase his expertise in lead generation and online marketing for the trades sector.
Learn more about Mike's experience and services at https://theleadguy.online or follow him on social media: